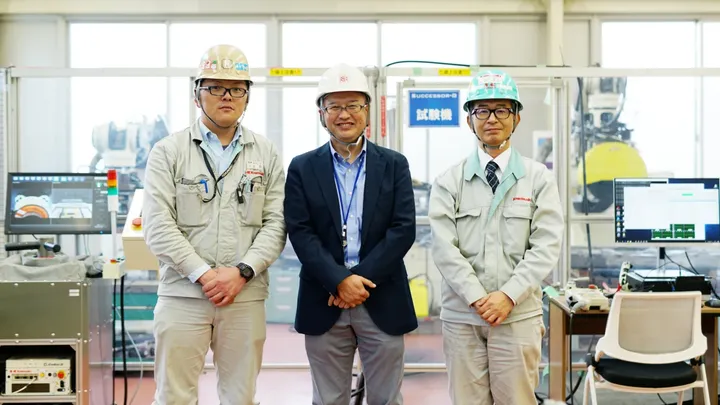
- BranżeElektronika
- AplikacjeUsuwanie materiału
- Seria RobotówSeria BX/BT
Kawasaki Heavy Industries, Ltd. Energy Solution & Marine Engineering Company, Harima Works
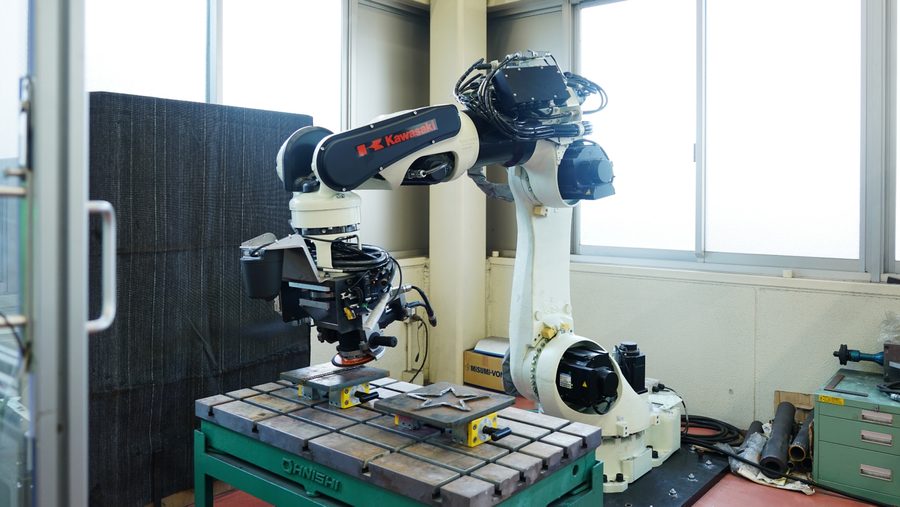
Although automation using robots and dedicated machinery are making progress, there is still a lot of work that requires human hands. For example, there is still a reliance on manual labor on the majority of grinder work, where a grindstone is rotating at high speeds, such as deburring of cast irons and grinding the gas cutting traces on steel plate. The Successor-G is the new robot system to improve the efficiency of that grinder work, which requires both time and labor, and to enable grinding of various shaped workpieces by touch sense feedback. Operations have already started at Harima Works of Kawasaki Heavy Industries, with the assumption of applications to actual workplaces.
Introduction background/issues:
Remote operation of work that relies on human sense
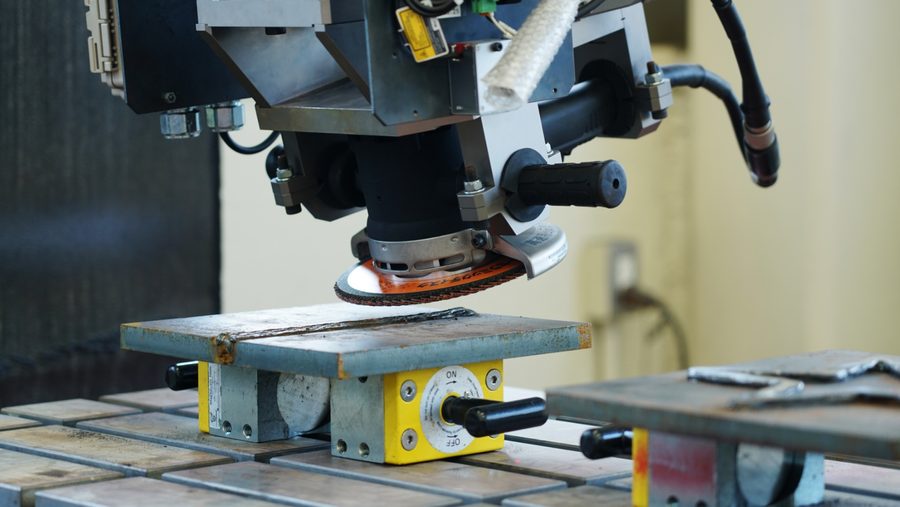
The robot density, which is the rate of the number of robots to that of workers, is increasing year by year. However, according to the International Federation of Robotics (IFR), even in the top three countries (Singapore, South Korea and Japan) in 2019 for the number of robots used per 10,000 employees), it is still less than 10%. The current situation is that there are still a lot of sectors where using robots is difficult. The system Kawasaki has announced as a new solution to cut into those sectors is the “Successor.” It is a remote collaboration system that creates the possibility of applying robots to work where automation has previously been thought to be difficult.
Assistant manager Takanori Kozuki of Manufacturing Promotion Section 2, Production Division, the Energy Solution & Marine Engineering Company, explains the Harima Works as follows.“Harima Works mainly handles large-scale structures. These are products such as the tunnel shield machine, LNG tanks, ship boilers, and aircraft autoclaves. In other words, they are products that support the infrastructure of society.”
The site area of the Harima Works is 450,000 square meters and it has easily over 1,000 employees. Why was the Successor-G introduced in this massive compound factory near the Seto Inland Sea?
Mr. Kozuki explains that, “The Successor was announced in 2017 and we decided to try using it within Kawasaki first. However, the introduction of industrial robots was already quite advanced at the Harima Works. There are already conventional types of robots in operation in processes such as welding and gas cutting, where there is a large amount of work and programming is easy.” So, what would be the optimal work for the introduction of a remote collaboration system? — Tasks were identified from the main work at the Harima Works and each task was considered. Mr. Kozuki explains that, “For example, the areas where the application of robots is difficult are ① work relies on the human senses and skills (= programming is difficult), ② work that is not feasible from the viewpoint of costs and times (requiring many sensors, teaching time, equipment modification, etc.), or ③ non-mass-produced products (order-made single items or products with slightly different parts). In our work here, typical items were grinder work for grinding and polishing.”
Introduction effects/solutions:
Continuous work cuts the work time in half
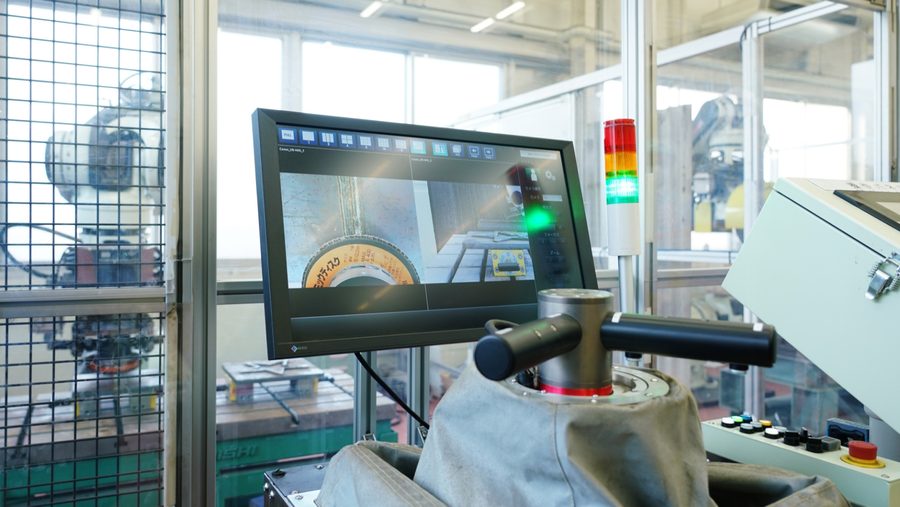
For finishing work (to make the required dimensions to the specification and good appearance) of comparatively large workpieces, automation has still not progressed and the majority of the work relies on human workers. Specially, grinder work is a heavy work, where the workers must wear a helmet, glasses, a dust mask, ear plugs and leather gloves. They must also hold a heavy grinding tool and the work involves ibration, noise, sparks and dust. As Mr. Kozuki explains, it is work that requires labor and time, and “There are restrictions on continuous working time by organizations related to industrial accident prevention. There are also guidelines requiring rest time for a specified period after the work.” To reduce the burden of the grinder work and improve the efficiency, it was decided at the Harima Works to apply the Successor-G for grinding gas cutting traces remaining on steel plates. The target workpiece is three steel plates of 50 mm thick and 4-meter square steel plates joined together. The grinding work previously took between 1.5 and 2 days to complete.
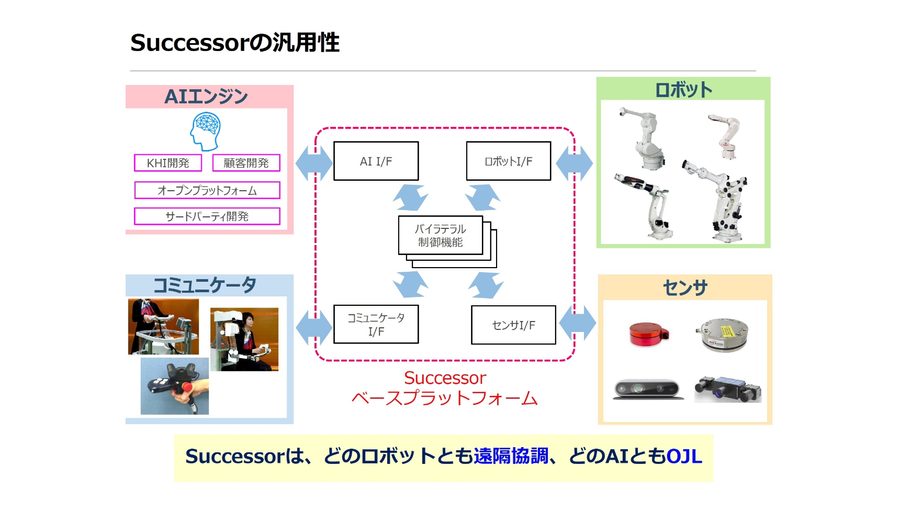
The flow of the grinding and polishing work using the Successor-G is as follows. First, move the robot arm from the point zero to the work start position with the program on the robot side, Switch to the Successor-G synchronizing operation mode, Grip the handle of the remote control device called the communicator, Press the simultaneous operation start button (At this time, the robot movements are synchronized with the movements of the worker), Press the ON button for the grinder, and Move the handle to the front, rear, left and right for the polishing work. Another feature is that the worker can perform the grinder work with just button operations and handle operations. “To have the operator focus on the work itself as much as possible, the operation of the robot has been made as simple as possible,” says, Takanori Kiritoshi, manager of Design Section 1, Transfer Equipment Department, Energy Solution & Marine Engineering Company,
Both the communicator and the robot are equipped with a force sensor to control the pushing force of the grinder and to receive the feedback from the robot to the worker’s hands. Mr. Kiritoshi explains, “The difficult part was how closely we could feedback the actual feeling of the work. The handle used this time was intentionally given a feeling of weight of approximately 500 grams. When we made it zero for lighter operations, we often have ‘no feeling of operating it’ from the worker. The force of the handle can be changed as required using the parameters, so it is also possible to set it to suit the preferences of the worker.”
Using the Successor-G enables the worker to operate from a spark- and dust-free, remote place. The worker needs protective apparatus and can concentrate on the work in a comfortable environment. In addition, the vibration is not transmitted to the hands, so continuous work is possible. As a result, the work time for one set of workpiece has been reduced from around 1.5 to 2 days to half the time. Mr. Kozuki says, “The burrs, cutting traces and bumps on cast iron are all different. It is necessary to check the state of the polishing and grinding visually while proceeding with the grinder work, so it cannot be handled with programming. Rather than a teaching playback, the remote collaboration of the Successor-G made the work possible with a robot.”
Future prospects and plans:Further expansion for applications of the Successor-G
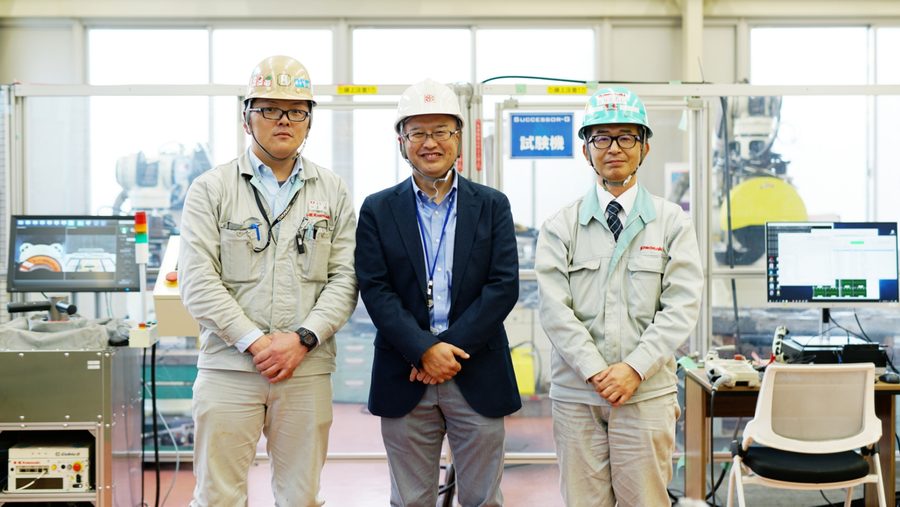
Mr. Kozuki looks back that, “In the workplace, some workers soon got accustomed to the operation of the Successor-G, but some others had an uncomfortable feeling.” Mr. Kozuki says, “There were the feeling of the actual work and the feeling of the remote work. To fill the gap between these two, in addition to adjustment of the force on the handle as mentioned previously, we also used an eye tracker and repeated fine adjustments of the camera position in line with the sight during the work.”
Various testing is currently being repeated with the goal of further expanding the functions of the Successor-G. Users say that, “Because we are going to install a robot, we want to improve the grinding efficiency.” In response to this request, a compact grinder is being developed that has equivalent capabilities to a heavyweight swing grinder that is used suspended on a hoist or the like. Element tests are being implemented for the robot operated remotely.
As Mr. Kozuki says, “The Successor-G can learn the robot movements taught through remote operations, So, if the operations of a skilled worker is learned and replayed, then I think it will also become possible to learn that skill through the robot.” Furthermore, a proof of concept using local 5G was also started in October 2020. Looking forward to the era of smart factories, we are aiming to perform work from a remote building or a location far away. The workers will be able to operate the robot from a comfortable office between two factories equipped with local 5G, or between a factory and a construction site connected with optical communications.—the Successor-G is continuing to advance in preparation for that era.
― Company information Company name :Kawasaki Heavy Industries, Ltd. Energy Solution & Marine Engineering Company, Harima Works Representative :Representative Director, President and CEO, Yasuhiko Hashimoto Established: October 1896 Capital: 104,484 million yen Core business: Manufacturing and sales of marine vessels, railway cars, aircraft, motorcycles, gas turbines, gas engines, industrial plants hydraulic equipment, robots, etc. Employees: 36,691 Offices: Tokyo Head Office: 1-14-5, Kaigan, Minato-ku, Tokyo Kobe Head Office: 1-1-3, Higashikawasaki-cho, Chuo-ku, Kobe, Hyogo Prefecture Website :https://www.khi.co.jp ― Robot system installed System model :Successor-G Features: A remote control type grinder robot system that can be used without teaching for the grinding of welded structures and burr removal and surface finishing processing on cast iron